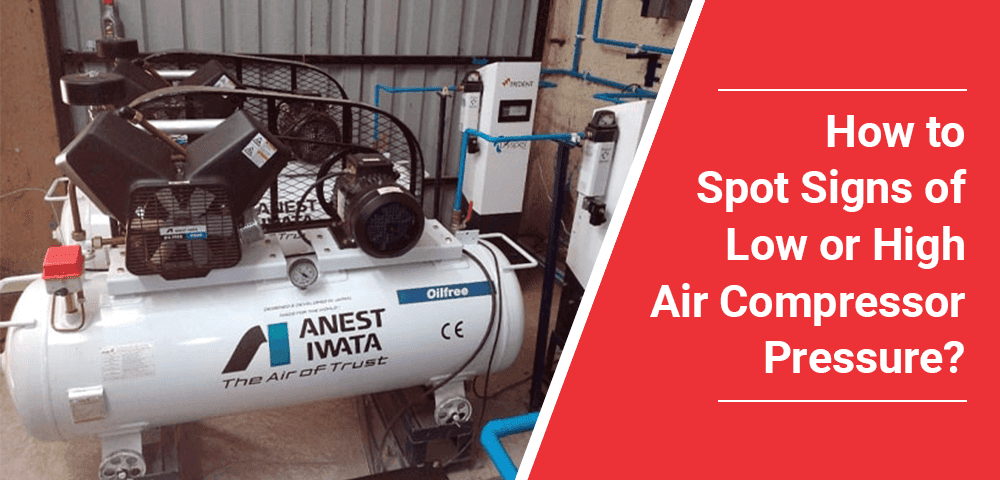
Air compressors play a pivotal role in industrial operations, as they offer an efficient power source for a variety of equipment across industries. Maintaining and controlling compressed air pressure levels is essential in industries to ensure optimal performance and safety of the equipment.
Monitoring air compressor pressure levels on a regular basis is necessary to identify issues affecting performance and improve efficiency. Running the compressor at high pressure can increase efficiency in the short term, but it can also decrease productivity, shorten the compressor’s lifespan, and damage its internal systems. In contrast, operating the low pressure compressors can have vice versa effects. Neglecting regular maintenance can also increase the risk of accidents.
Thus, maintaining air compressor pressure levels is crucial for efficient and safe operations in many industries. Proper pressure levels ensure efficient operation, and product quality, and minimize maintenance costs and downtime. To achieve optimal performance, it is essential to regularly monitor and maintain air compressor pressure levels. Let’s have a look at the signs of the difference between high pressure and low pressure air compressors.
A] Signs of Low Air Compressor Pressure
Listed below are two warning signs that your air compressor pressure has fallen too low and that you need to take measures to fix the issue with your industrial air compressor before it affects your productivity.
1. Slow or weak output
Slow or weak output is a sign of low air compressor pressure that can result in poor system performance, causing slower output and reduced efficiency in the production process. Failure to properly maintain the air compressor can contribute to slower tool operation, weaker pneumatic impact, or longer filling times. It’s important to regularly monitor the compressor, including checking for displaced belts, identifying damages, and examining pump rings, motor capacitors, and air demand filters for leaks.
To prevent slow output and maintain compressor efficiency, regular servicing and maintenance are necessary. The air compressor’s output can be monitored by data logging. Data logging can also help identify slow or weak output and help you take corrective actions to prevent damage and improve process efficiency.
2. Difficulty in starting
When the air pressure is not sufficient, an air compressor may struggle to start. This issue can be caused by various factors such as insufficient pressure, a faulty motor, leaks in the system or electrical problems. A worn or damaged motor can also cause difficulty in starting an air compressor, which can impact its overall efficiency and performance. Lack of lubrication or issues with the motor’s bearings or windings is another cause which leads to difficulty starting air compressors.
Additionally, if the electrical system is not functioning properly, the compressor may not receive the power it requires to start. This can be due to issues with the wiring, a malfunctioning switch, or problems with the circuit breaker.
B] Signs of High Air Compressor Pressure
High air compressors pressure can damage not only the air compressor but also the equipment it is powering. Let’s have a look at the signs that your air compressor pressure may be too high.
1. Artificial Storage Creation
Artificial storage is created when the requirement of compressed air is greater for an intended application, but your air compressor doesn’t have sufficient storage. This can damage the air compressor overtime and reduce its lifetime.
So, if your air compressor is creating artificial storage with increased pressure, the air pressure is likely too high. Especially when the machine has poor control over pressure, it results in a shortage of storage. This shortage of storage leads to the creation of artificial storage with high pressure.
Poor compressor discharge pressure, machinery faults, and leaks are other signs of high air compressor pressure. It is important to monitor the pressure of your air compressor and address the issues if any immediately to prevent any damage to the system or injury to a person.
2. Safety valve release
When the air compressor pressure exceeds safety levels, the safety valve opens and releases excess pressure to prevent damage to equipment and ensure safety. If the pressure switch fails to shut off the compressor at the cut-out pressure, the safety valve works as a backup mechanism for pressure regulation. The pressure relief valve is a critical piece of safety equipment for air compressors, and it opens when the pressure inside the compressor becomes too high.
The pressure relief valve opening can be a sign that excessive pressure is building up inside the compressor. If the safety valve is leaking, it may be releasing pressure all the time, which is an indication of a high pressure air compressor. By monitoring the performance of the air compressor and checking for signs of high pressure, industries can take corrective action to prevent damage and improve the efficiency of their processes.
3. Damaged or burst hoses
The hose can get damaged or may burst out due to the high air compressor pressure. High pressure fluctuations is one of the signs of high air compressor pressure which may occur as a result of poor pressure control on the machine. Therefore, it’s essential to get the regular maintenance done to prevent such issues.
Additionally, other signs of high air compressor pressure are any physical damage or leaking around the hose, slipped belts, faulty controls, and internal wear and tear due to high air pressure. Proper maintenance of air compressors can avoid these issues.