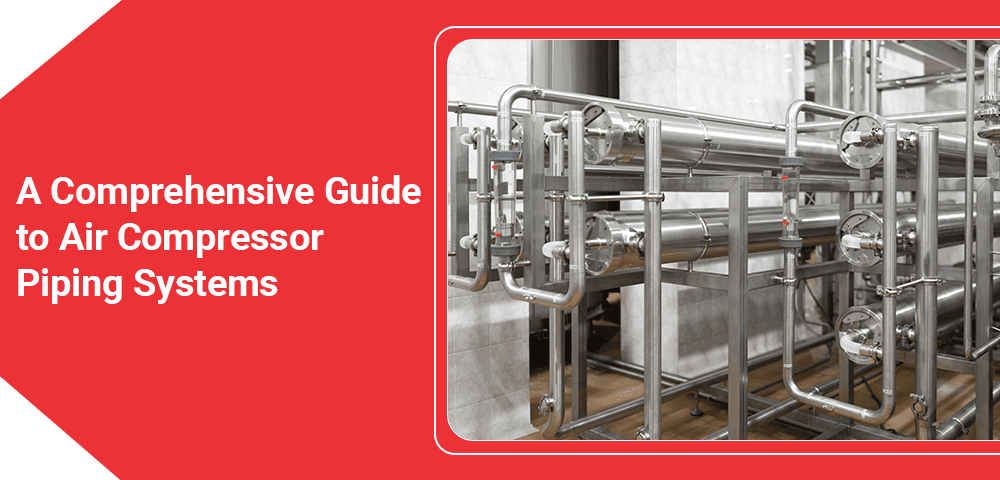
Compressed air is an essential component in many industries and businesses. The air compressor piping system provides a safe and efficient way to carry compressed air to the point of use from the compressor. Therefore the piping system should be designed in such a manner to deliver optimum compressed air with sufficient volume, quality, and pressure to power the components. When the air compressor piping systems are optimized it proves as an advantage including reduced energy costs, increased equipment lifespan, and improved production efficiencies.
In this blog, we have covered five different types of compressed air piping system based on various materials and how to optimize piping layout to improve the compressed air efficiency leading to reduced idle time.
A] What Are Compressed Air Pipping Systems? How Do They Work?
A compressed air piping system is a network of pipes that provides compressed air to various applications in industries such as agriculture, manufacturing, mining, food processing, and construction. Industrial air compressors supply a clean and reliable energy source via this piping system to pneumatic tools, machinery, conveyor systems, operating controls, and more.
The system works by using the pressure of the compressed air to push it through the pipes. The air dryer removes moisture from the compressed air, which helps to prevent corrosion and damage to equipment. The valves control the flow of air, and the connectors connect the piping system to the equipment that needs compressed air. The fittings and components, such as filters, regulators, and lubricators, help maintain the quality of the compressed air and ensures it meets the specific requirements of each application.
Here are the essential components of a typical industrial compressed air piping system:
- Piping: This tube carries compressed air from the system to various locations in the facility where it is required.
- Pipe Fittings: Fitting such as connectors, adapters, elbows, tees; help to connect the pipes and ensures the right direction of compressed air.
- Hangers and Supports: Brackets, clamps, and hangers are like the backbone of a piping system providing sufficient support and stability. They ensure proper alignment and reduce any shaking caused by vibrations.
- Isolation Valves: These valves works as a replacement to isolate compressed air without affecting the system when there is a need for prompt maintenance or repairs.
- Pressure Relief Valves: When there is too much pressure building up in the system, these valves automatically release the extra pressure. This prevents overpressurization and protects the components from getting damaged due to excessive pressure.
- Check Valves: These valves keep things running smoothly, by allowing the compressed air to move forward only in one direction and block it from going backwards. This way, mishaps are prevented.
- Pressure Regulators: These regulators monitor the pressure at various points in the system and make adjustments as needed, ensuring that each area receives the appropriate amount of air.
- Filters and Separators: Filtration systems work together to remove unwanted elements such as particles, oil, and water from the compressed air. This maintains the air quality and prevents any harmful substances from reaching downstream equipment.
- Condensate Drains: These devices eliminate built-up condensate, which is water, from the system. This prevents any moisture-related problems from occurring and keeps the system operating efficiently.
- Manifolds and Branches: These components take the compressed air from the main pipeline and distribute it to various places within the facility.
If you are curious about how air compressors operate, read our blog : How Do Air Compressors Operate? What are their Applications?
B] Types of Compressed Air Piping Systems Based on Material
1. Stainless Steel Piping Systems
Stainless Steel Pipes are the most resistant to corrosion which makes it durable unlike other compressor piping system. While quality makes the stainless steel piping system expensive amongst other piping systems, but its worth the investment. However, it’s important to note that working with stainless steel requires proper tools, an experienced person and special installers due to its challenging cutting and welding processes. Certain industries such as manufacturing, automotive, aerospace and heavy machinery mandatorily require stainless steep piping systems in their application because for them it is essential to keep rust and particulates out of the air stream.
2. Copper Piping Systems
If you are looking for a corrosion-free piping system for applications that require superior air quality, a copper piping system is the best option. As compared to steel piping, copper pipes are light in weight, easy to install, and boast a wide range of fittings, making them a preferred choice in the industry. Also, their smooth interior ensures a solid laminar flow, enhancing their performance. The only disadvantages are its high cost and it can get damaged from vibration and thermal expansion, causing leaks and air contamination. This piping system are widely used in industries such as construction, HVAC, refrigeration, and healthcare facilities.
3. Plastic Piping Systems
Plastic Piping Systems are cheap, light in weight, easier to install and non-corrosive. PPCH is a great piping material which is used during high pressure of water, whereas CPVC can be easily shaped and flexible then PPCH. Also, the piping you choose should be durable to withstand years of use. Plastic pipes are most often used in industry applications such as food and beverage, pharmaceuticals, laboratories, and water treatment facilities.
4. Aluminum Piping Systems
Aluminium piping systems feature non-corrosive properties similar to stainless pipe, except that aluminum pipes are much lighter and easier to install. This piping requires no anchoring or support and can be installed without the use of welding, threading, or brazing. Because of its wide size, this piping system may transport compressed air, vacuum, and inert gas, as well as high-pressure air or fluids. Due to its smooth interior, line losses are decreased, resulting in lower maintenance costs when compared to alternative materials. Industries across various sectors, including electronics, automotive assembly, packaging, and textile manufacturing, widely adopt aluminum piping systems for their operations.
5. Composite Piping Systems
Composite piping systems are made with mixture of Fiber Reinforced Plastic (FRP) and other composite materials, resulting in low maintenance, easy handling, and installation, while offering exceptional durability in harsh conditions. However, these pipes can be a bit fragile, making them more prone to damage and not as flexible as some other options. Though many industries such as petrochemical, oil and gas, marine, and wastewater treatment plants are using this piping system due to corrosion resistance and lightweight construction.
C] Optimizing Piping Layout for Improved Pressure Efficiency
1. Designing an Efficient Piping Layout
Maintaining pressure efficiency requires an efficient compressed air piping architecture. To begin, examine the facility’s layout to determine the best placements for compressors and storage tanks to reduce pressure loss. Then, to dramatically reduce pressure loss and maximize pressure efficiency, keep piping lines short and direct, eliminating needless curves and maintaining straight pathways. Make your plans flexible enough to allow for future changes and development.
2. Pipe Sizing and Diameter Selection
For an efficient compressed air system, proper pipe sizing is critical. It entails taking into account airflow requirements as well as pressure drop. Designers utilize charts and algorithms to calculate the appropriate piping diameter based on variables such as run length, maximum CFM, and minimum PSI. It is critical to ensure adequate flow and minimal pressure loss, which includes avoiding inadequate pipes, which result in higher energy consumption owing to increased pressure drop. On the other hand, avoiding oversized pipes improves efficiency and lowers expenses.
3. Proper Support and Pipe Anchoring
Proper support and pipe anchoring are critical concerns when designing and installing a compressed air piping system. Adequate supports, such as appropriately positioned pipe anchors and alignment guides, minimize drooping and misalignment while ensuring system stability. Correct pipe anchoring reduces vibration and movement, assuring long-term performance and avoiding premature wear and damage. Thermal movement can be accommodated by using expansion joints or flexible connectors while maintaining system integrity.
4. Locating and Managing Pressure Drops
Identifying potential pressure drop spots requires knowledge of valves, fittings, and obstacles, as well as PSI readings to construct a pressure map. Using smooth turns, fittings of the right size, and shorter, straight pipe runs can help reduce pressure drops. Implementing pressure regulators can be used to keep pressure consistent throughout the system, while control devices can be utilized to modify pressure based on demand.
5. Separating Different Air Quality Needs
Specific requirements for each section can be determined by segmenting air quality needs and distinguishing dry air, oil-free air, and other uses. This enables the installation of suitable filtration and treatment systems to remove contaminants and provide optimal air quality. Additionally, protecting the system’s integrity and performance involves preventing contaminated air from air compressors using suitable isolation and control techniques.
These steps can not only help improve pressure effecicecy but also help increase the durability of your air compressor. If you are looking to make your air compressors last longer, refer to our blog: Tips For Extending Air Compressor Life Across Industries.
Conclusion
For any industrial plant, a well-designed compressed air pipe system is an essential investment. A well-optimized air compressor system increases pressure effectiveness, lowers energy usage, and guarantees dependable performance. In today’s competitive market, controlling expenditures, including energy costs, is crucial. Your electricity bill is an area where you can have some control, and a high-efficiency compressed air pipe system can help reduce these costs significantly.
If you would like to learn more about air compressors or air compressor piping systems, don’t hesitate to reach out to us.