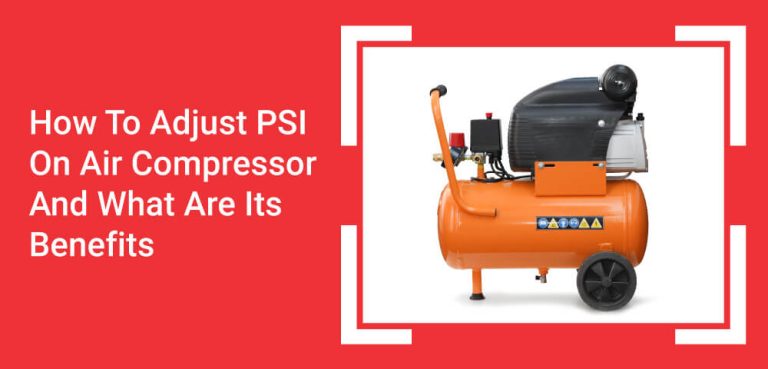
Knowing how to adjust the PSI on air compressors has several benefits, including improved performance and longevity of the air compressors. However, adjusting the air pressure can be a tricky task, which is why many people avoid it. This can have drastic consequences on the machine’s productivity and the safety of the workers and should not happen.
To help you with this problem, we have brought to you this detailed guide explaining how you can easily adjust your air compressor’s PSI. We will also be explaining why you should always set the air pressure according to your needs.
A] The Step-By-Step Process Of Adjusting PSI On Air Compressors
Step 1: Unplug The Air Compressor And Drain The System
Before beginning the process, make sure the power supply is cut off. This helps to prioritise safety and accidental activation during maintenance. You must also drain the industrial air compressor to ensure the system is completely decompressed. You need to do this using the drainage valve to avoid any sudden releases. This air compressor pressure adjustment valve will have a knob which allows you to adjust it accordingly. Close the drain valve once you have emptied the chamber.Â
Step 2: Adjust The Springs
Once you have unplugged and drained the system, remove the cover of the pressure switch. They would be most likely held in their place by a few screws. Make sure to use the right tools to avoid damaging the components. Refer to the label, datasheet, or operating manual to do it correctly. There, you will find a large spring, which will be responsible for adjusting the cut-in and cut-out pressure. If there is a smaller spring present, it will most likely be used for adjusting the differential pressure. The springs are connected to screws which help to adjust them. This is an important process for making precise adjustments to the PSI.
Step 3: Set The Cut-in And Cut-out Pressure
The cut-in pressure is the minimum pressure at which the air compressor will start again. In contrast, the cut-out pressure is the upper limit of the pressure at which point the air compressor will stop. These are also known as reset points or failing pressure, and are necessary for maintaining safety. Use a suitable screwdriver to turn the screw clockwise, which increases the cut-in pressure. Turning the screw counter-clockwise decreases the cut-in pressure. Remember to do this slowly and carefully to avoid any mistakes.Â
Step 4: Turn On The Compressor
Plug in the compressor and turn it on. Let the pressure build up in the chamber and pay attention to the pressure gauge. The air compressor will continue to fill the tank until it has attended the cut-out pressure; at which point it should automatically stop. If this is not the case, simply note the pressure at which it stops. This stage helps you determine if all the adjustments are working as intended or do they need further work. You should definitely check if the compressor is able to reach the desired pressure in the required time.Â
Step 5: Slowly Release The Compressed Air
Once the cut-out pressure is tested, you can drain the valves again. Make sure you open the drain valve, slowly and carefully to avoid any hazards. Keep an eye on the pressure gauge while the compressed air is slowly released. Once the pressure reaches the new cut-in point, the air compressor should restart. If the compressor does not turn on at the set air pressure, let it drain completely and note down at what point it reactivates.Â
Step 6: Fine-Tune To Set The Correct Pressure
This step is only necessary if the compressor does not start or stop automatically at the desired pressure. Adjust the respective screws according to the test results you just collected. Remember to rotate the screws clockwise to set the cut-in or cut-out pressure higher. This fine-tuning process is necessary to automate the air compressor and ensure optimal performance.
Step 7: Turn On The Compressor And Check
Reconnect the air compressor once again and let it fill. Monitor the air pressure gauge and compare it to your set cut-in and cut-out pressure. If the process still needs some adjustments, repeat step six again. Continue this process until you reach the optimal performance.
B] Benefits Of Operating On Optimal Air Pressure
1. Improved Efficiency And Lower Electrical Wastage
Using the air compressors at the right pressure ensures it does not have to work more than it needs to. This can be counterproductive, as most of the extra compressed air it produces will go to waste. Efficient use of air compressors lowers operating costs and also boosts productivity. Additionally, this is excellent for the environment and also reduces energy bills. Using as little energy as required will reduce your carbon footprint.Â
2. Better Safety
Air compressors generate highly pressurised air that is capable of powering industrial pneumatic tools. If not handled properly, this pressure can cause serious injuries to anyone standing nearby. If the air compressors do not stop at a set cut-out pressure they could cause ruptures and explosions, hurling high-velocity projectiles. Also, adjusting PSI on compressors according to the requirements has less chance of causing fires or short circuits.Â
3. Reduced Wear and Tear
Operating the air compressors at improper pressures causes heavy vibrations and places unnecessary stress on various components. Under such conditions, components such as valves, hoses, and seals can wear and tear more rapidly than they would otherwise. Using the air compressor according to the industry’s requirements also keeps the motor in optimal condition. This improves the air compressor’s longevity and lowers the frequency of maintenance-induced downtime. If minimising wear and tear is very important for you, you can go for an oil-free reciprocating air compressor and an oil-free scroll air compressor. The absence of oil in the system ensures longevity.
4. Minimising Noise Pollution
Air compressors create a lot of noise when they are on. This is greatly amplified when they are operating on higher or lower pressure than required. Noise pollution can be hazardous for workers and other people on the floor. It can lead to partial or complete loss of hearing. Setting air pressure on compressors at optimal pressure creates a safer and better working environment.
5. Efficient Heat Management
When operating on optimal pressure, the air compressor experiences less friction and strain, leading to lower heat generation. By effectively reducing overheating, you can vastly improve the compressor’s lifespan and productivity. If you are facing constant overheating problems, read our blog on combating air compressor overheating: causes and fixes, to learn more.
Conclusion
Knowing how to adjust air pressure on an air compressor can be a game changer for your organisation’s productivity. This guide gives you the step-by-step process of adjusting your air compressor’s pressure. Use this along with the manufacturer’s manual to avoid any mistakes. Make sure to unplug the compressor and drain the compressed air using the drain valve before beginning the process.
If you are interested in purchasing a high-quality air compressor for your industrial pneumatic needs, contact us today! Bimpex is a leading supplier of all types of air compressors.